Plastic has been in the news a lot recently, and not because scientists have found an exciting new use for it, or have invented a new polymer. No, it is the environmental impact of plastic that makes headlines these days.
The build up of waste plastics is a major environmental catastrophe, one that will have a far-reaching impact on all forms of life on this planet. And our reliance on plastics in so many industries means that transitioning away from plastics is highly unlikely in the short term.
Finding new and better ways of producing and dealing with plastics is therefore one of the key challenges facing industrialized societies in the 21st century, and much hinges on our ability to overcome it.
Confronting the Problem
But the issue isn’t just that plastics, once used, are being discarded in record numbers. According to usave, a conservation collective, it is also that plastic production is often extremely wasteful, and drives up global carbon use.
One of the reasons for this is the fact that processing plastics is an intensive, multi-step process. From the distillation of crude oil in refineries to the moulding of products on the assembly line, plastic goes through many stages of development.
This makes plastics energy intensive to produce, which in turn drives up the amount of carbon needed to turn crude oil into usable products.
While long-term solutions will need to incorporate a complete overhaul of the energy sector and a move toward renewable solutions, in the short term one of the most effective ways to reduce the impact of plastics on the environment is to adopt more energy efficient ways of producing plastic.
How Technological Innovation is Providing Solutions
Improving production efficiency for plastics is an overarching project that the entire industry needs to take seriously, but due to the complexity of the process, piecemeal solutions are one of the best ways for individual actors to approach the issue.
For example, when it comes to heating, drying, and cooling bulk solids, many manufacturers are turning to the latest technology thermal transfer heat exchangers to get the results they need with a lower investment of energy overall.
New heat exchangers that use ceramic plates rather than belt coolers or fluid bed coolers can sometimes cut energy use by as much as ninety percent, and can even return waste energy back into the factory grid to reduce waste even further.
While this may seem like a small aspect of plastics production, heat exchange is often one of the most inefficient and wasteful aspects of production, so improvements made on this front can have a lasting impact on the overall energy efficiency of plastics production in the 21st century.
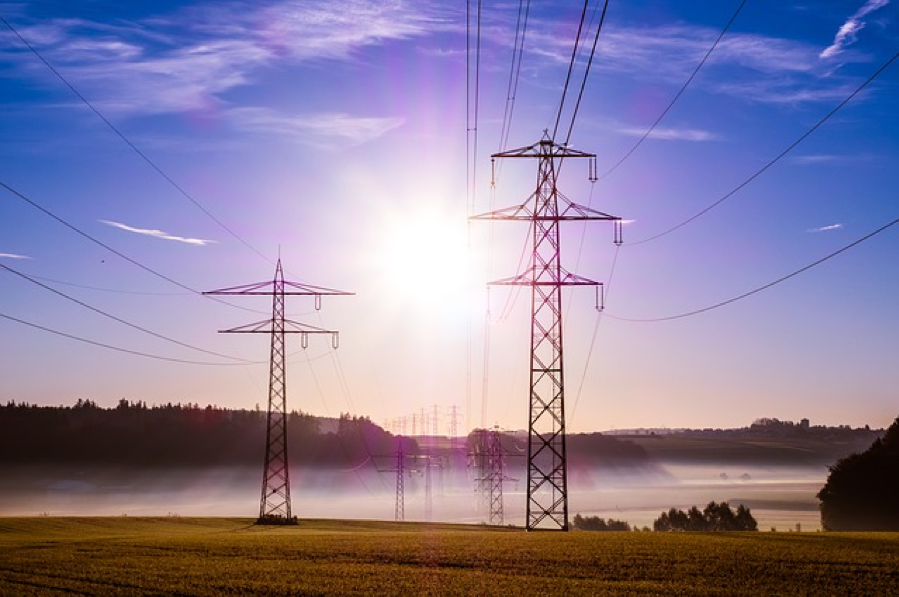
Last year, National Geographic published a story revealing that plastic is now being found even at the deepest points in the ocean floor: the Mariana Trench. Clearly, humans need to find a way of dealing with their addiction to plastic.
But one of the first steps toward a more environmental approach to plastic is to find ways to produce it more efficiently. Fortunately, with the help of better heat exchange technology, plastic producers are starting to move toward more sustainable ways of creating the plastics we use every day.